Platform L2
Self-leveling underlayment designed to facilitate flat floors and hold slope
Features
- Hydraulic cement underlayment powered by portland cement based Synthecem technology
- Low surface preparation
- Install 1/4″ to 2+″ NEAT (in isolated areas, in a single lift)
- Foot traffic in 3-4 hours
- Reduced dust
- Suitable for light trade traffic
- Slope from 1″ to feather over 5 ft
- Smooth, flat and hard surface suitable for vinyl, LVT, carpet, engineered wood, ceramic and more
(well bonded, clean, dry, sound and stable)
- Concrete, concrete plank
- Existing patching and leveling materials
- Sound gypsum
- Steel pan
- Cement or epoxy terrazzo
- Well bonded existing flooring such as VCT, ceramic tile
- Qualified adhesive residue (non soluble, non PSA)
FOR PROFESSIONAL USE ONLY
Reference the floor covering and adhesive manufacturers documentation to verify suitability of Platform L2 as a subfloor for the flooring system (any adhesive used for concrete is generally suitable for L2). Follow the directions of the flooring and adhesive manufacturer to determine the maximum allowable moisture content (RH) or transmission of the substrate. If the moisture content (ASTM F-2170) or moisture vapor transmission rate (ASTM F-1869) of the substrate exceeds the requirements of the flooring system, utilize an approved 100% epoxy moisture vapor mitigator prior to installation of the Platform L2.
Honor all moving joints. Complete crack and substrate repairs prior to installation. Consult an engineer for required joints and crack repairs prior to installation. Contact Technical Services for required surface preparation on installations that will be exposed to high rolling loads or high point loads.
Maintain a minimum of 50ºF during the pour and for 72 hours after the pour. Acclimate the material to a minimum of 55ºF prior to mixing. To maximize flowability and working time, utilize cool water when temperatures exceed 85ºF.
For installation over hydronic heating systems utilize a minimum of 1.5” of material, with ¾” of material above the hydronic system. Platform L2 is compatible with and accepts the direct application of, urethane, moisture cure and other typical floor covering adhesives.
Platform L2 can be applied in two lifts to a maximum depth of 2" NEAT monolithically and up to 3" deep NEAT in isolated areas.
It is recommended clean, washed and SSD (saturate surface dry) 1/4 - 3/8” pea gravel is utilized in areas deeper than 2”. Applications deeper than 3” must be extended with aggregate. Extend L2 up 50% (by weight - 25 lbs pea gravel per 50 lbs L2). Ensure pea gravel is thoroughly mixed in (encapsulated) by the L2.
Surface Preparation
All Substrates must be sound, clean, dry and free of contaminants (oil, dirt, laitance etc.) that may interfere with adhesion. Areas of the floor that do not exhibit a tensile pull strength greater than 100 psi are not suitable and must be mechanically removed to a sound, stable base and subsequently repaired prior to application of Platform L2. Do not use solvents, acids, chemical adhesive removers to prepare the substrate. All bond breaking substances (cure residues, excess salts from silicates etc.) must be removed prior to priming. Completely vacuum all dust and debris from the substrate prior to priming with designated Platform primer.
Gypsum substrates must exhibit a sound surface, be free from dust and surface weakness prior to application of the primer.
Non-soluble adhesives must be scraped to a well bonded residue. Water soluble adhesives must be removed mechanically to the substrate. Verify type of adhesive prior to mechanical removal to ensure adhesive containing asbestos is not introduced into the environment. Follow all local, state and federal laws for removal and disposal of adhesive or flooring materials containing asbestos. Platform L2 is not for use as a suitable means to encapsulate residue of hazardous materials.
Wood floors must satisfy local building codes, utilize exterior grade plywood, suitable OSB or other resistant to water, and be free from deflection. The wood must be free of contaminants (oils, wax, dirt etc.) that could function as bond breaker prior to application of the primer. Platform recommends use of reinforcing lath when installing L2 over wood subfloors, contact technical support for details.
Substrate Priming
Prime properly prepared substrate with an Platform Primer P360 prior to the application of L2, Prime properly prepared porous (concrete) and non-porous substrates (adhesive residue, epoxy terrazzo, ceramic tile etc.) with Primer P360 by soft tipped broom (porous) or 3/8” nap roller (non-porous). Carefully read Primer data sheet to ENSURE Primer is utilized diluted (porous substrates) or undiluted (non-porous substrates) per given substrate.
Platform L2 is very flowable and will flow through any exposed voids. To avoid material flow in undesirable areas, seal voids or penetrations with a rapid setting patch or expanding foam. L2 has tremendous bonding properties, place tape or bond breaker on vertical surfaces that will contact the Platform L2. Provide a barrier between Platform L2 and metallic construction (e.g. heating pipes).
When applying Platform L2 on wood substrates,double prime with P360 NEAT and utilize reinforcing lath stapled to the wood floor after priming.
Mixing
Water: 4 - 4.75 US Qts (3.75 - 4.5 L) per 50 lbs (22.7 kg)
Mix Time: 2 minutes with minimum 650 rpm drill or through pump.
Over-watering and/or under mixing (failing to generate adequate shear) will result in lower ultimate compressive strengths.
Add designated clean, potable water to a clean mixing barrel, add the powder and mix at the designated speed for 2 minutes. Ensure all material is homogenous, and no dry lumps or unmixed material is at the bottom of the mix. During mixing, keep the paddle below the surface of the material to reduce introduction of excess air into the mix. Once mixed, pour onto the substrate immediately to maximize material flow and placement time.
Pumping
Platform L2 may be mixed and/or pumped with most standard batch or inline mixing/pumping equipment. Contact Platform Technical services for pump questions.
Material Application
Immediately after mixing is complete pour the mix on the substrate, rake to the required depth and smooth using appropriate tools (smoother or porcupine roller). When placing mixed material, maintain a wet edge, always pouring back into the leading edge of the previous placement.
Drying Time
Do not used forced air to assist in drying Platform L2, but do provide for adequate ventilation and circulation of air. Platform L2 generally hardens to accept light foot traffic 3 - 4 hours after placement. Avoid construction traffic for a minimum of 16 - 24 hours (temperature dependent).
L2 is self drying, do not wet cure or use curing or sealing compounds. To facilitate drying, ensure rooms where L2 is installed have air circulation. Do not introduce heavy airflow to the surface of L2 until after 16-24 hours of drying. Temperature, humidity and airflow will impact drying time. The use of a moisture meter is recommended to verify readiness for flooring. Multiple areas should be surveyed to ensure dryness throughout. Use of a Delmhorst G-79 and a reading of 5% moisture content or lower, or a GE® Protimeter moisture meter such as the Aquant. In the RF (Radio Frequency) mode a ready of 180 or lower indicates suitable dryness for any floor covering.
General drying guidelines assuming ambient temps of 70ºF with air circulation (Cooler temperatures and/or high humidity will increase drying times);
Breathable Flooring Systems
Depth Dry time required before installing flooring
0 - 1” 16 hours (next day)
1 - 2” 36 hours (1.5 days)
2 - 3” 60 hours (2.5 days)
Non-Breathable/Impervious Flooring Systems
Depth Dry time required before installing flooring
0 - 1/2” 24 hours
1/2 - 1” 48 hours
1” 48 hours plus 36 hours for each additional 1/2’
Internal testing of the latest generation of high performance underlayments including L2 indicates bond of cementitious adhesives like thinset and patch is significantly enhanced with the use of a primer. When utilizing cementitious patch or setting materials(thinset) enhanced bond can be realized by priming dried L2 with P360 primer diluted at 3:1 (water:primer). For enhanced bond and resistance to the movement of moisture and alkalinity prime the L2 with P360 diluted.
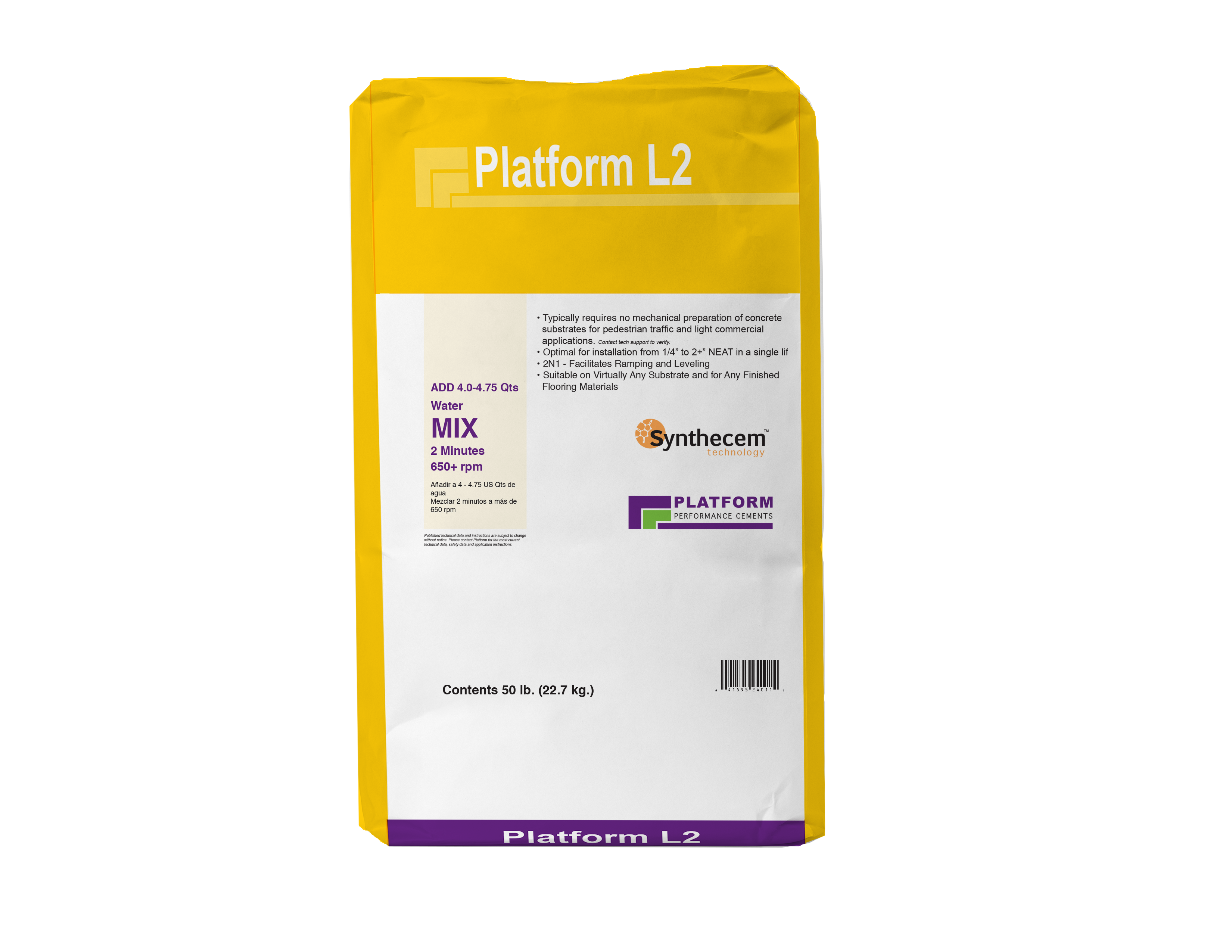
